Long'an Conch Cement Co., Ltd. Cement Bulk Metering System Technical Transformation Project
发布日期:2021-07-29 浏览次数:799
1. Project overview
The 5000t/d cement clinker production line of Long'an Conch Cement Co., Ltd. is located in Nanxu Town, Long'an County, Guangxi Province. In 2020, the plant planed to add 3 sets of bulk metering systems at the bottom of the three original bulk cement silos. Three sets of KXT(SZ)-250 cement bulk metering system from our company were selected. The plant completed the installation and commissioning of one set of metering system in December 2020. The equipment has accurate measurement and is in good operating condition. The plant plans to complete the installation and commissioning of the remaining two sets of metering system around the 2021 Spring Festival.
2. Previous problems
Before the completion of the technical renovation project of the bulk metering system, there are mainly the following problems:
(1) Bulk packaging and measurement are separated, with many management links, low efficiency, and easy to be interfered by human factors;
(2) The bulk packaging process is mainly manual operation, with high labor intensity, poor working environment and high potential safety hazards;
(3) There is basically no online measurement for loading, and estimation is based on experience. In order to avoid overloading, repeated loading and unloading of bicycles is more common, especially in areas with strict road load limit inspections. This phenomenon is particularly prominent, causing secondary pollution and low efficiency;
(4) There are many agglomerations of cement in the bulk storage, and there is a problem of jamming at unloading, which affects the quality of cement delivered.
3. Customer needs
(1) The bulk cement and weighing are completed synchronously, and the measurement accuracy reaches ±1%;
(2) Simplify the work process and realize one-key operation on the HMI;
(3) Use the original flow aid and dust collection equipment, retain the on-site vibrating screen and sampler, and minimize the cost of transformation.
4. Transformation plan
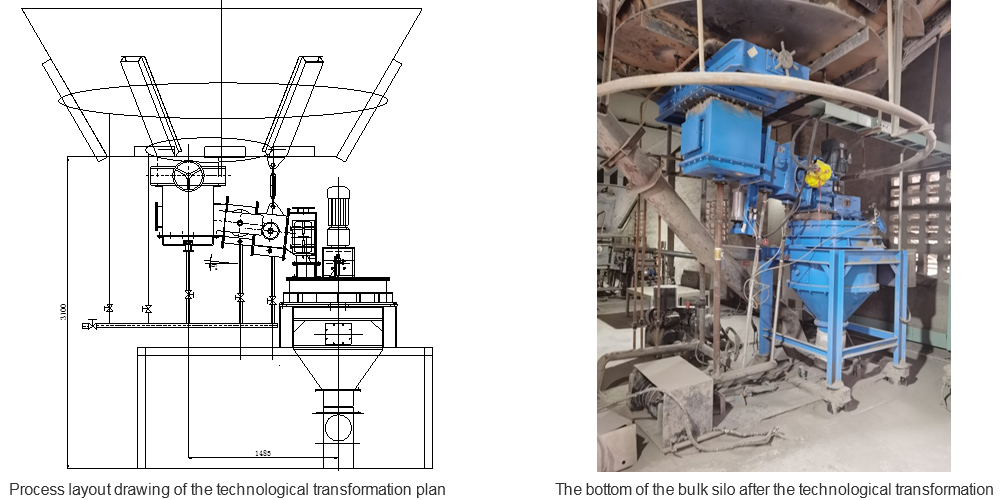
(1)Because the installation height on site is not enough, the original bulk silo cone and the silo bottom plate are packaged. In order to avoid unsmooth unloading, inflatable boxes are reasonably arranged on the silo cone and the silo bottom plate (see Figure 5 and Figure 6), and Roots blower is used. The fan is used as a flow aid air source;
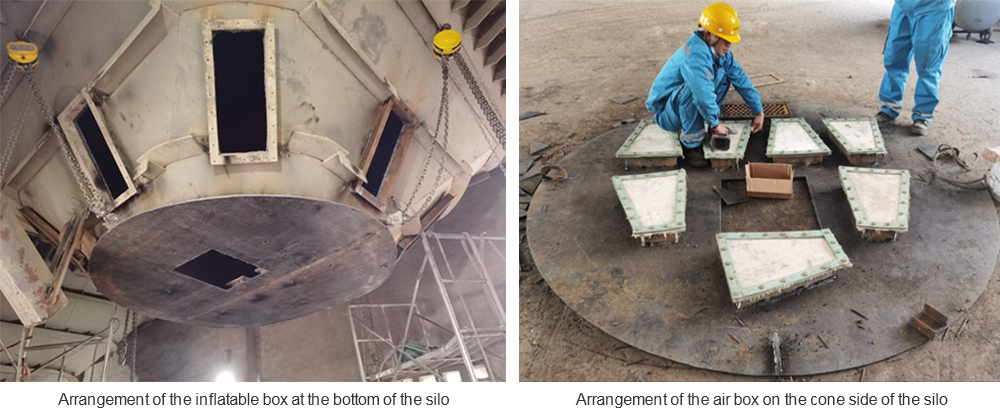
(2) Install spiral gates, inflatable distribution boxes, pneumatic switch valves, pneumatic flow valves, bulk metering systems in sequence at the bottom of the silo. The outlet of the metering system and the original vibrating screen equipment are softly connected by a canvas clamp, and the vibrating screen outlet is connected to the bulk machine. ;
(3) In response to the problem of more cement agglomeration, under the premise of temporarily not arranging clearing the silo, the manufacturer added a clump breaking device at the bottom of the cement product silo bottom discharge valve group, and retained the original vibrating screen on the bulk machine as The last protective barrier;
(4) In terms of system control, in addition to the control cabinet, a touch-type operation screen is equipped on site, and one-button operation completes all loading links such as unloading, metering, control, loading, and dust collection. The design of human-computer interaction interface is friendly. The touch screen contains a loading report design program, which supports the upload and export of reports, which is convenient for data statistics and information push. At the same time, the system reserves an interface, which can be connected to the ERP system, video surveillance system and smart card system in the later stage to realize unattended operation and further improve the efficiency of bulk shipping.
5. Analysis and summary
Figure 7 Typical bulk truck flow curve
The plant's first KXT (SZ) cement bulk system was completed in December 2020. After the equipment was put into operation, the loading flow was relatively stable (see Figure 7), and cement agglomeration was greatly reduced. Most of the loading data show that the measurement accuracy reaches ±1% (typical loading data is shown in Table 1), and the equipment is operating in good condition.
Table 1 Typical loading data
License number |
Display loading volume t |
Actual loading t |
Absolute deviation t |
Measurement error % |
8090 |
40.33 |
40.22 |
0.11 |
0.27% |
9710 |
62.91 |
62.54 |
0.37 |
0.59% |
1091 |
47.05 |
47.08 |
-0.03 |
-0.06% |
2002 |
58.79 |
58.44 |
0.35 |
0.60% |
2069 |
58.24 |
57.68 |
0.56 |
0.97% |
7575 |
32.79 |
32.86 |
-0.07 |
-0.21% |
1781 |
49.33 |
49.38 |
-0.05 |
-0.10% |
9978 |
42.68 |
42.34 |
0.34 |
0.80% |
0626 |
46.5 |
46.22 |
0.28 |
0.61% |
1057 |
56.42 |
56.20 |
0.22 |
0.39% |
Through technological transformation, the factory has solved the long-standing problems of complex cement bulk processing, low efficiency, high labor cost, multiple management links, and difficulty in overload control, and achieved the established technological transformation goals. The plant's subsequent two sets of bulk metering systems plan to complete the technical transformation during the Spring Festival maintenance period in 2021.
1. Project overview
The 5000t/d cement clinker production line of Long'an Conch Cement Co., Ltd. is located in Nanxu Town, Long'an County, Guangxi Province. In 2020, the plant planed to add 3 sets of bulk metering systems at the bottom of the three original bulk cement silos. Three sets of KXT(SZ)-250 cement bulk metering system from our company were selected. The plant completed the installation and commissioning of one set of metering system in December 2020. The equipment has accurate measurement and is in good operating condition. The plant plans to complete the installation and commissioning of the remaining two sets of metering system around the 2021 Spring Festival.
2. Previous problems
Before the completion of the technical renovation project of the bulk metering system, there are mainly the following problems:
(1) Bulk packaging and measurement are separated, with many management links, low efficiency, and easy to be interfered by human factors;
(2) The bulk packaging process is mainly manual operation, with high labor intensity, poor working environment and high potential safety hazards;
(3) There is basically no online measurement for loading, and estimation is based on experience. In order to avoid overloading, repeated loading and unloading of bicycles is more common, especially in areas with strict road load limit inspections. This phenomenon is particularly prominent, causing secondary pollution and low efficiency;
(4) There are many agglomerations of cement in the bulk storage, and there is a problem of jamming at unloading, which affects the quality of cement delivered.
3. Customer needs
(1) The bulk cement and weighing are completed synchronously, and the measurement accuracy reaches ±1%;
(2) Simplify the work process and realize one-key operation on the HMI;
(3) Use the original flow aid and dust collection equipment, retain the on-site vibrating screen and sampler, and minimize the cost of transformation.
4. Transformation plan
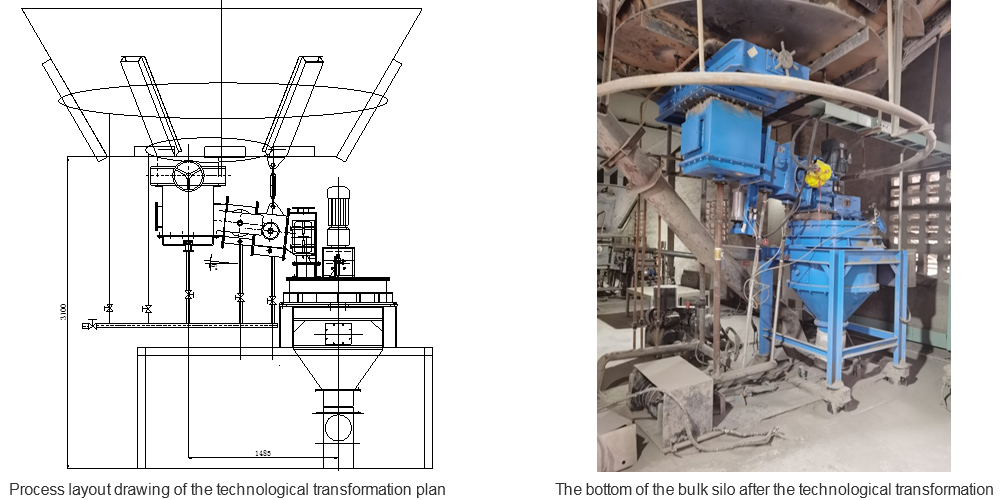
(1)Because the installation height on site is not enough, the original bulk silo cone and the silo bottom plate are packaged. In order to avoid unsmooth unloading, inflatable boxes are reasonably arranged on the silo cone and the silo bottom plate (see Figure 5 and Figure 6), and Roots blower is used. The fan is used as a flow aid air source;
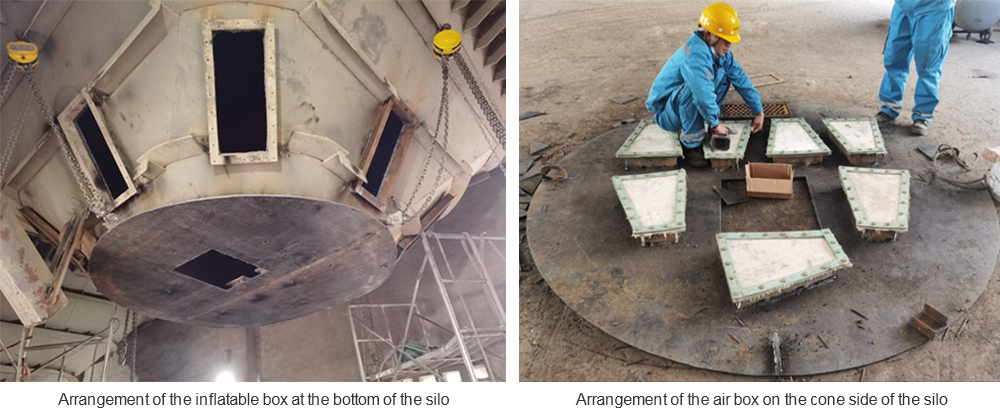
(2) Install spiral gates, inflatable distribution boxes, pneumatic switch valves, pneumatic flow valves, bulk metering systems in sequence at the bottom of the silo. The outlet of the metering system and the original vibrating screen equipment are softly connected by a canvas clamp, and the vibrating screen outlet is connected to the bulk machine. ;
(3) In response to the problem of more cement agglomeration, under the premise of temporarily not arranging clearing the silo, the manufacturer added a clump breaking device at the bottom of the cement product silo bottom discharge valve group, and retained the original vibrating screen on the bulk machine as The last protective barrier;
(4) In terms of system control, in addition to the control cabinet, a touch-type operation screen is equipped on site, and one-button operation completes all loading links such as unloading, metering, control, loading, and dust collection. The design of human-computer interaction interface is friendly. The touch screen contains a loading report design program, which supports the upload and export of reports, which is convenient for data statistics and information push. At the same time, the system reserves an interface, which can be connected to the ERP system, video surveillance system and smart card system in the later stage to realize unattended operation and further improve the efficiency of bulk shipping.
5. Analysis and summary
Figure 7 Typical bulk truck flow curve
The plant's first KXT (SZ) cement bulk system was completed in December 2020. After the equipment was put into operation, the loading flow was relatively stable (see Figure 7), and cement agglomeration was greatly reduced. Most of the loading data show that the measurement accuracy reaches ±1% (typical loading data is shown in Table 1), and the equipment is operating in good condition.
Table 1 Typical loading data
License number |
Display loading volume t |
Actual loading t |
Absolute deviation t |
Measurement error % |
8090 |
40.33 |
40.22 |
0.11 |
0.27% |
9710 |
62.91 |
62.54 |
0.37 |
0.59% |
1091 |
47.05 |
47.08 |
-0.03 |
-0.06% |
2002 |
58.79 |
58.44 |
0.35 |
0.60% |
2069 |
58.24 |
57.68 |
0.56 |
0.97% |
7575 |
32.79 |
32.86 |
-0.07 |
-0.21% |
1781 |
49.33 |
49.38 |
-0.05 |
-0.10% |
9978 |
42.68 |
42.34 |
0.34 |
0.80% |
0626 |
46.5 |
46.22 |
0.28 |
0.61% |
1057 |
56.42 |
56.20 |
0.22 |
0.39% |
Through technological transformation, the factory has solved the long-standing problems of complex cement bulk processing, low efficiency, high labor cost, multiple management links, and difficulty in overload control, and achieved the established technological transformation goals. The plant's subsequent two sets of bulk metering systems plan to complete the technical transformation during the Spring Festival maintenance period in 2021.