Application example of intelligent drive system of Yichun Red Lion steel cord belt elevator Key words:Intelligent drive, Many Ethernet interfaces,Red Lion Group
发布日期:2021-07-23 浏览次数:772
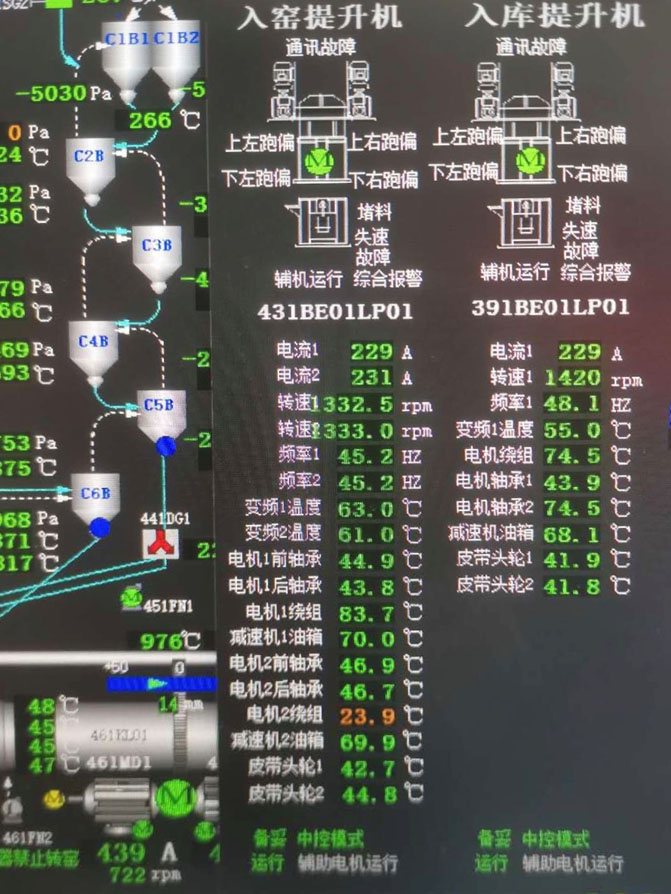
1.Project Introduction
Yichun Hongshi Cement Co., Ltd. built a 4500t/d intelligent cement clinker production line in Jiangxi, and the NTGD1000 and NTGD1250 steel cord belt elevators of our company are selected for the kiln and storage of the production line. About the two elevators, the elevator for kiln is dual drive, and the both elevators are equipped with our intelligent drive system. The intelligent drive system of this project has been put into operation for more than a year and is running well. Besides, for the dual drive elevator, Current difference between two motors is lower than 3A, and the balance is great.
2.Current Status of Elevators for Kiln and Silo
For key positions such as kiln and silo elevators, most companies do not realize networking and rely on point-to-point communication to achieve "hard connection". This method can neither guarantee the accuracy of data, but is also prone to accidental events caused by on-site interference and shutdown seriously affects production efficiency. There are also some companies that implement partial networking of equipment through the PROFIBUS protocol, but the protocol still has the following problems: 1) PROFIBUS is only a bus standard that uses automated production. Compared with the advanced control bus designed by Ethernet, it has poor openness and compatibility; 2) PROFIBUS cannot meet the functions related to Ethernet operation, fault analysis and network security diagnosis by connecting the communication between the master station and the slave station, and the real-time performance is not high; 3) PROFIBUS relies on professional remote modules, dedicated communication cables and connectors, and the use cost is high; 4) Although PROFIBUS is widely used in the traditional automation industry, it cannot be used flexibly in the wave of advancement of intelligent equipment because its protocol is not open, resulting in reduced equipment scalability.
Based on the above factors, we proposed a elevator control system based on PROFINET bus. The cumbersome execution system and instrumentation on site can communicate with the host computer through this open real-time communication standard based on Ethernet, which can guarantee the data transmission rate and actual effect. It can also ensure the security issues in the process of remote data collection through its own fault diagnosis.
3.The Overall Design of The System
The overall design of the system is based on Siemens PLC development, using a three-level multi-layer network integration method, using temperature, deviation detection, speed detection and other sensors to collect the bottom layer data of the elevators, and some signals are uploaded to the PLC after proper transmission and conversion; The transmission part is driven and controlled by a powerful inverter, and realizes data collection and intelligent communication of the underlying motor through the bus protocol; On the one hand, the PLC will synchronize the collected protocol to the HMI through the Ethernet protocol for on-site monitoring and operation; on the other hand, through the more secure PROFINET protocol and remote host computer communication, it can realize the remote operation, maintenance and monitoring of the elevator control system.
4.Main Functions of The System
The elevator control system based on bus technology is used to solve the real-time data collection, fault diagnosis, intelligent control and load balancing of the hoist used in key positions. Its main functions are as follows:
The "smart communication" between double-drive elevator is realized through the DDCS protocol, and load balancing, energy saving and consumption reduction are realized based on the intelligent algorithm of torque.
Realize PLC's intelligent control, operation monitoring, fault protection and data collection of the drive system through the MODBUS protocol.
Through the PROFINET protocol, the elevator equipment control system and the upper computer management system can interact across network segments, so that the computer system can transfer key data to the intelligent system in time, avoiding the management negligence, and improving production efficiency.
Figure 2. Control system interface
5.Summary
The elevator intelligent control system based on bus technology realizes the interconnection and intercommunication of production and management between equipment through the bus, and provides a flexible, efficient and safe terminal solution for the integration of key equipment into smart factories. This project not only effectively integrates into the remote monitoring system of the user's upper computer, but also realizes the integration of data into the intelligent early warning system of the whole factory, reduces manual intervention in the production process, and improves the adaptive adjustment ability.
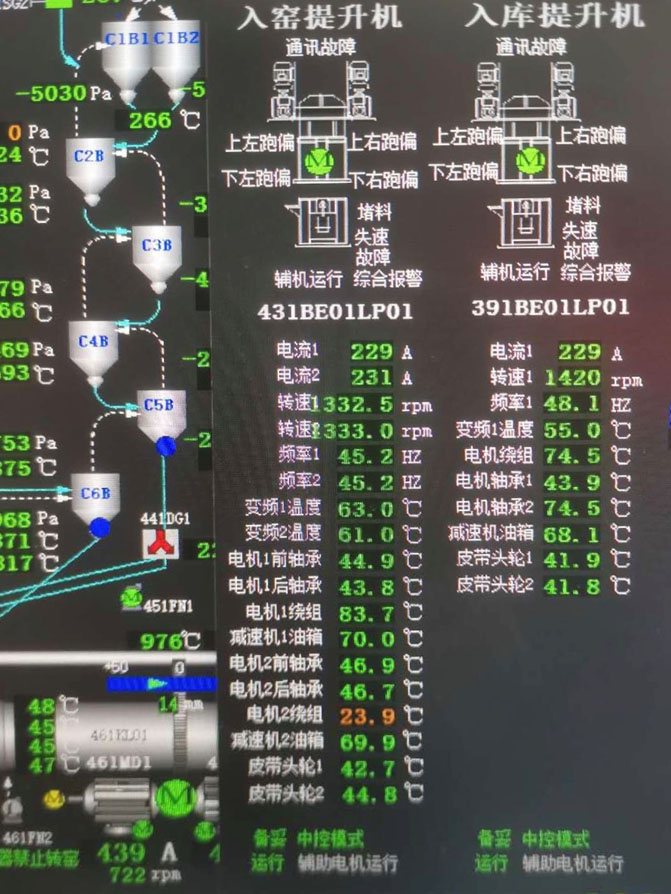
1.Project Introduction
Yichun Hongshi Cement Co., Ltd. built a 4500t/d intelligent cement clinker production line in Jiangxi, and the NTGD1000 and NTGD1250 steel cord belt elevators of our company are selected for the kiln and storage of the production line. About the two elevators, the elevator for kiln is dual drive, and the both elevators are equipped with our intelligent drive system. The intelligent drive system of this project has been put into operation for more than a year and is running well. Besides, for the dual drive elevator, Current difference between two motors is lower than 3A, and the balance is great.
2.Current Status of Elevators for Kiln and Silo
For key positions such as kiln and silo elevators, most companies do not realize networking and rely on point-to-point communication to achieve "hard connection". This method can neither guarantee the accuracy of data, but is also prone to accidental events caused by on-site interference and shutdown seriously affects production efficiency. There are also some companies that implement partial networking of equipment through the PROFIBUS protocol, but the protocol still has the following problems: 1) PROFIBUS is only a bus standard that uses automated production. Compared with the advanced control bus designed by Ethernet, it has poor openness and compatibility; 2) PROFIBUS cannot meet the functions related to Ethernet operation, fault analysis and network security diagnosis by connecting the communication between the master station and the slave station, and the real-time performance is not high; 3) PROFIBUS relies on professional remote modules, dedicated communication cables and connectors, and the use cost is high; 4) Although PROFIBUS is widely used in the traditional automation industry, it cannot be used flexibly in the wave of advancement of intelligent equipment because its protocol is not open, resulting in reduced equipment scalability.
Based on the above factors, we proposed a elevator control system based on PROFINET bus. The cumbersome execution system and instrumentation on site can communicate with the host computer through this open real-time communication standard based on Ethernet, which can guarantee the data transmission rate and actual effect. It can also ensure the security issues in the process of remote data collection through its own fault diagnosis.
3.The Overall Design of The System
The overall design of the system is based on Siemens PLC development, using a three-level multi-layer network integration method, using temperature, deviation detection, speed detection and other sensors to collect the bottom layer data of the elevators, and some signals are uploaded to the PLC after proper transmission and conversion; The transmission part is driven and controlled by a powerful inverter, and realizes data collection and intelligent communication of the underlying motor through the bus protocol; On the one hand, the PLC will synchronize the collected protocol to the HMI through the Ethernet protocol for on-site monitoring and operation; on the other hand, through the more secure PROFINET protocol and remote host computer communication, it can realize the remote operation, maintenance and monitoring of the elevator control system.
4.Main Functions of The System
The elevator control system based on bus technology is used to solve the real-time data collection, fault diagnosis, intelligent control and load balancing of the hoist used in key positions. Its main functions are as follows:
The "smart communication" between double-drive elevator is realized through the DDCS protocol, and load balancing, energy saving and consumption reduction are realized based on the intelligent algorithm of torque.
Realize PLC's intelligent control, operation monitoring, fault protection and data collection of the drive system through the MODBUS protocol.
Through the PROFINET protocol, the elevator equipment control system and the upper computer management system can interact across network segments, so that the computer system can transfer key data to the intelligent system in time, avoiding the management negligence, and improving production efficiency.
Figure 2. Control system interface
5.Summary
The elevator intelligent control system based on bus technology realizes the interconnection and intercommunication of production and management between equipment through the bus, and provides a flexible, efficient and safe terminal solution for the integration of key equipment into smart factories. This project not only effectively integrates into the remote monitoring system of the user's upper computer, but also realizes the integration of data into the intelligent early warning system of the whole factory, reduces manual intervention in the production process, and improves the adaptive adjustment ability.